Flexel International Ltd.'s Production Programme
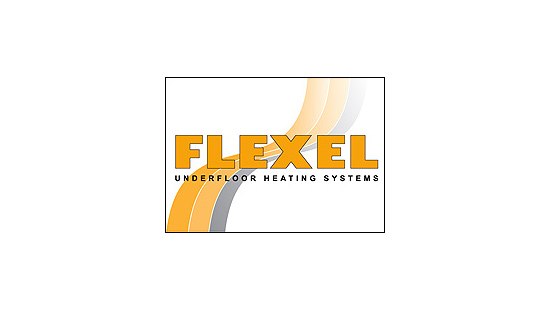
The concept of Flexel carbon heating elements dates back to 1965. The first product, developed by ICI, was a carbon heating element denominated Mark 1. The product was further developed in the course of several years and since the year 1975 its production continued under the denomination Mark 2 manufactured by Thermaflex Ltd. The present Mark 2 heating element, made by Flexel International Ltd., is composed of a strip of glass fibre cloth on which a layer of homogenized carbon/graphite is applied. Electrical energy is brought into the heating film using two copper strips and is transformed into thermal energy. Mark 2 is manufactured in surface density 100 W/sqm–1000 W/sqm.
Due to its long-time reliability and growing demand, Mark 2 has been continually manufactured and used as a heating element for electric radiant panels, infra-red cabins (saunas), caravan heaters, heating panels and heating cassetes, etc.
Late in 1993, Flexel International Ltd. launched a new product – based on the present construction of polyester heating film. Thanks to its entirely new construction and effective technology, the polyester based heating film became a breakthrough in floor and ceiling heating systems.
The structure of polyester heating film can be seen in the following figure:
-
Polyester/polyethylene film
-
Copper strips
-
Silver plating (pure silver conductor)
-
Homogenized graphite
-
Polyester/polyethylene film
The polyester based films products are manufactured under the denomination Mark 3, 4 or 5. The construction principle of polyester films Mark 3, 4 and 5 is the same. The numbers just indicate a print pattern of homogenized carbon/graphite determined at customer's request (e.g. the heating film ECOFILM is the design Mark 4). The polyester films Mark 3, 4, 5 are manufactured in the supply density 60 W/sqm–300 W/sqm. Maximum temperature resistance (surface temperature) of the polyester films Mark 3, 4, 5 is 80 °C for long-term thermal load (max. 100 °C for short-term thermal load).
On introducing the new production of Mark 3, 4, 5 films based on polyester, Flexel became the sole company in the world capable of manufacturing both types of carbon based heating systems (heating elements based both on the glass fibre cloth and the printed carbon polyester film), therefore Flexel is the only company offering the entire range of products that are available on the market. This unique background contributes significantly to the fact that Flexel is one of the world leaders in the production of electric surface heating systems having a strong position in both the national and world markets. On the basis of long-term experience, the following analysis and comparison, has been prepared of both types of products currently available from Flexel International Ltd.
Mark 2 (carbon heating element based on a glass fibre cloth)
If this type of product is electrically insulated in materials other than a polyester/polyethylene film (e.g. mica based insulation materials), it can be used for the production of a heating element with higher linear inputs (W/lin.m.) and so a greater watt density than would be permitted in the case of polyester based insulation materials. The greater the watt density, the greater is the temperature stability required of the insulation materials used. Copper strips bringing electrical energy into the heating film are sewn on lateral sides of the carbon/graphite coated glass cloth.
Laminated Mark 2
For the standard insulation materials based on polyester/polyethylene, the operating temperature is limited by the maximum operating temperature (softening point) of this material. That means, if Mark 2 (a heating element based on a glass fibre cloth) is electrically insulated in a polyester/polyethylene film (so-called Laminated Mark 2), the operating temperature can be only selected up to the manufacture's specified continuous operating temperature. The manufacturing process of Laminated Mark 2 is significantly slower than the manufacture of the polyester films Mark 3, 4, 5 and for these reasons the Laminated Mark 2 is mainly used in restricted applications.
Printed Carbon Polyester Films Mark 3, 4, 5
The advantage of the printed carbon heating films Mark 3, 4, 5 (without a glass fibre cloth) is its greater flexibility and strength than that of the Mark 2 glass cloth based product.
Where the heating element is subjected to extreme handling and mechanical stress, e.g. bending, the printed carbon films Mark 3, 4, 5 are much more resistant than that of a glass fibre cloth element. Should the Mark 2 glass cloth element be subjected to extreme flexing the coated glass fibres may rupture. This potential damaging of the heating element would not occur with the polyester based Mark 3, 4 or 5. It is for this reason, the films Mark 3, 4, 5 are preferred for floor or ceiling heating where the finished product is used on building sites. In the polyester films Mark 3, 4, 5 copper strips bringing electrical energy into the heating film are laminated to the lateral sides of a conductive carbon layer and are in intimate contact with a silver strip conductor made from pure silver. This conductor ensures vertical and horizontal electrical conductivity and is so perfect that it is able to permit on its own the transfer of energy of up to 2 metres without the need of copper strips.This combination of systems of two conductors results in another advantage, i.e. efficient reduction of so-called contact resistance (electrical resistance between a copper strip and a conductive carbon layer). Another great advantage of the construction of the heating films Mark 3, 4, 5 is their versatility. These heating films can be designed to comply exactly with various applications at customer's request. The films are used in large surface floor and ceiling heating (ECOFILM F & C), for heating mirrors to prevent misting (ECOFILM MHF), in cultivation (soil heating in plant pots), in animal comfort (vivarium and aquarium heating technology) etc.
Examples of the use of heating films Mark 3, 4, 5 in various fields:
- floor and ceiling large surface heating with the ECOFILM F & C (Mark 4)
- reliable protection against mirror misting, e.g. in bathrooms (ECOFILM MHF with a self adhesive layer for easy installation)
- cultivation – soil heating
- animal comfort-vivarium and aquarium heating (Ultratherm heat strips)
As the manufacture of the heating films Mark 3, 4, 5 is carried out on an automated production line with automatic control based on the most advanced technology, their production capacity, quality and reliability are fully ensured. All these factors form an integral part of the business success of Flexel International Ltd. and its partners. Note: At the beginning of the year 2004 the company Flexel International Ltd. based in Scotland became a member of the Fenix Holdings Group S.A.
Written by:
W. Stenhouse, Flexel International Ltd.,
D. Bernatík, P. Kudelka – Fenix Group a.s.